Successfully shaping the digital transformation.
We have prepared a comprehensive program for you that will facilitate your digital transformation.
WORKSHOP
Get to know the Innovation and Learning Center and the technical possibilities of digital solutions in production.
CONSULTING
We help to identify the benefits, formulate goals and shape the path to digital transformation.
IMPLEMENTATION
In a pilot project you get to know our working methods. Here we lay the foundation for a long-term cooperation.
Potential analysis
In the potential analysis, we uncover opportunities for the successful implementation of digital solutions.
In personal discussions, expert interviews and inspections of your production facilities, we uncover the potentials with which you can achieve the greatest benefit from digitalisation.
Procedure in the potential analysis
Day 1
- Interview
- Interview with as many people involved in production and producction management as possible (factory managers, employees general managers)
- Factory Tour
- Inspection of the production to record the current level of digitalisation
- Digital Waste Walk
- Investigation regarding waste (lean approach), targeted questions about waste and deficits of analogue production
- Follow-up
- Processing the interviews and the factory tour in preparation for the workshop on day two
Day 2
- Workshop
- Presentation of the analysis method and presentation of the results
Prioritisation of the digitalisation potentials
Creation of the digitalisation-roadmap - Q&A
- Answering open questions and discussion
Consulting
Benefit from our know-how, our experts and our international members in the Innovation and Learning Center Aachen.
Implementation projects
In recent years, we have been able to assist many companies in their digital transformation.
Let our projects inspire you. .
Implementation of a predictive maintenance system
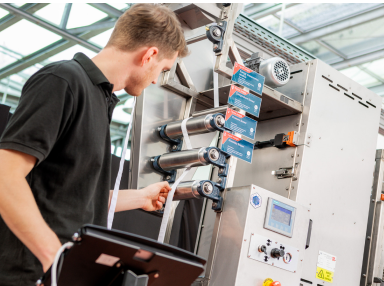
Reduction of machine downtimes by applying predictive maintenance in the production facilities. By constantly monitoring the condition of the machines with regard to wearing parts, it is possible to predict impending failures and avoid unplanned shutdowns.
In-line quality control system using image processing
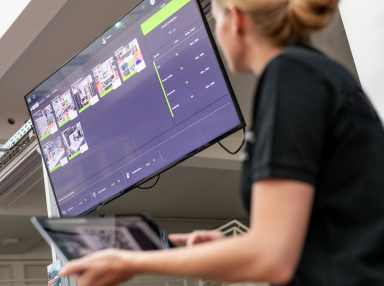
Introduction of AI-based image processing systems for in-process quality monitoring. Integration of automatic alerts and action recommendations to dashboards.
Management training for the digital transformation in the company
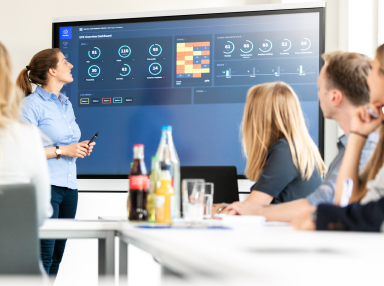
Education and consulting on digital technologies in carbon fibre production and setting up a "digital taskforce" in the company. Introduction to digitalisation solutions and capability building at operator and C-level.
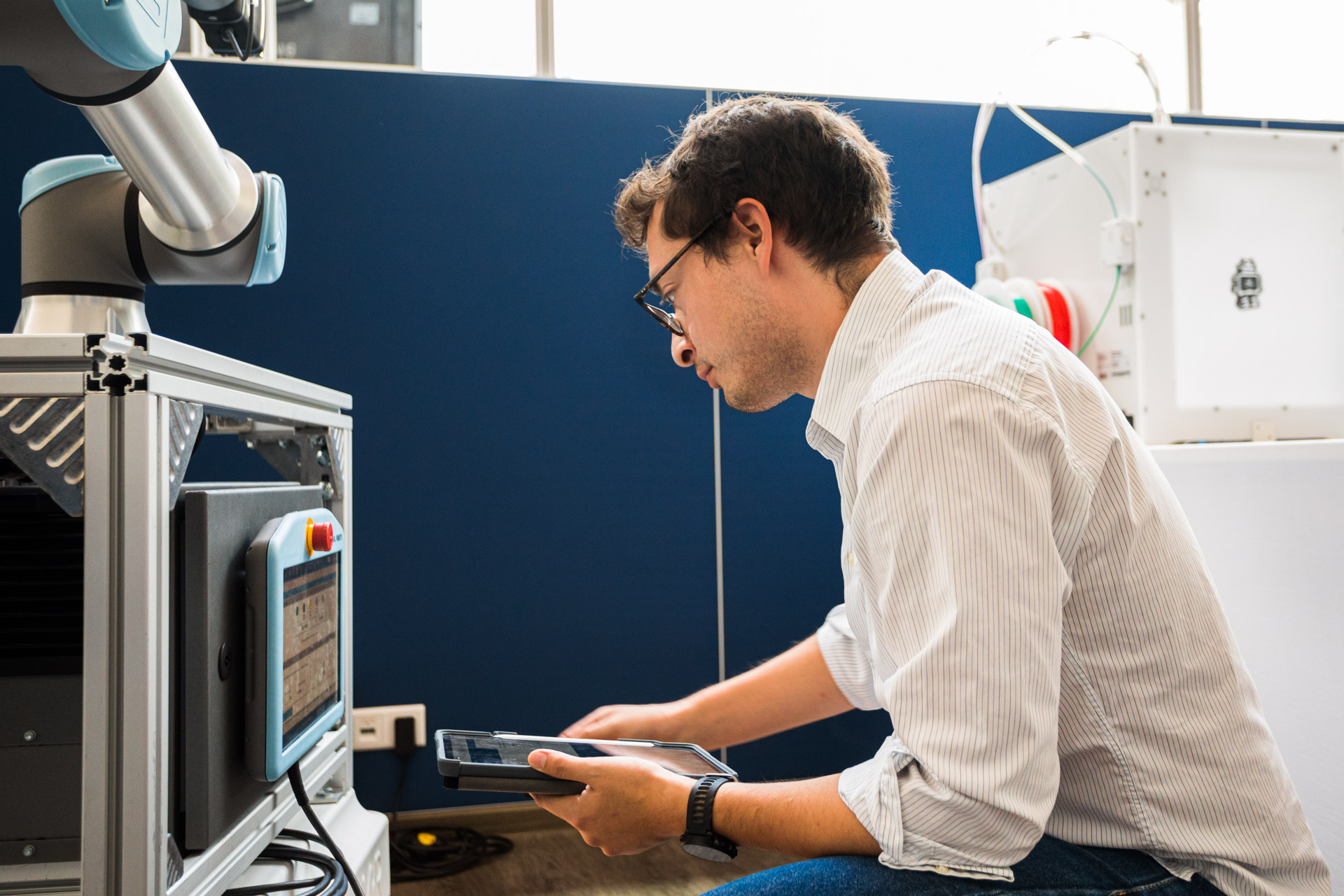
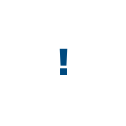